piezobrush® PZ3-i cold plasma device for improved adhesion of ink, glue, etc.
The piezobrush® PZ3-i has been specially developed for integration into new and existing production lines. It enables intuitive operation, comprehensive process control in automated production processes and is therefore compact, safe and efficient. With a maximum power consumption of 18 W, it uses the Piezoelectric Direct Discharge (PDD®) technology to generate highly efficient cold plasma.
Fields of application
- Inkjet, marking and pad printing
- Bonding processes with epoxy, polyurethane and cyanoacrylates etc.
- Potting and dispensing technology
- Joining and assembly technology
- Laboratory and medical technology
- Packaging technology
- Microbiology, microfluid and food technology
Highlights
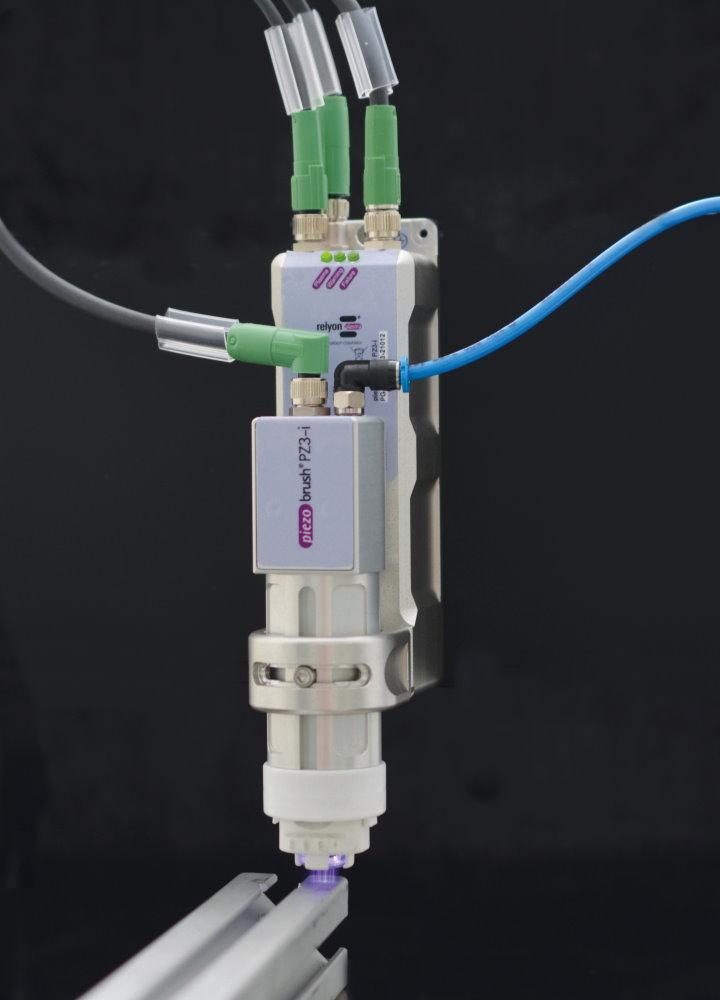
Possible use cases
Activation of surfaces of a wide variety of base materials
Optimization of bonding, printing and lamination processes
Surface treatment of plastics, glasses, ceramics, metals, composites and natural materials
Selective improvement of the wettability of a wide variety of surfaces
Fine cleaning of surfaces
Alternative to chemical primers, flame treatment processes and mechanical roughening
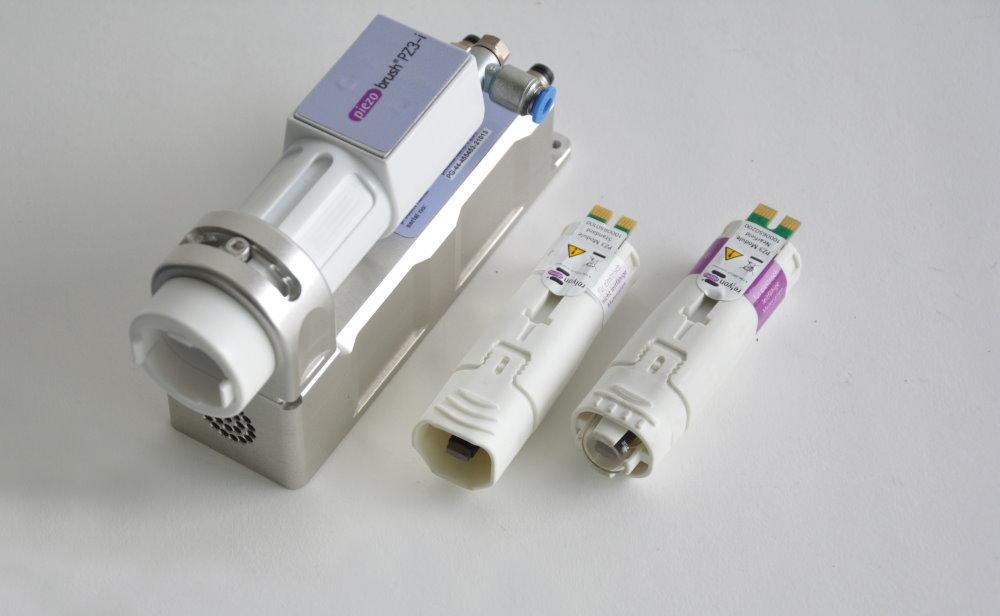
Use of the piezobrush® PZ3-i
The piezobrush® PZ3-i can be easily integrated into new and existing production lines. The typical treatment speed varies depending on the application. For finest cleaning, a treatment speed of 1 - 15 mm/s is possible, for gluing processes of 10 - 150 mm/s and for printing processes of 10 - 150 mm/s. Different surfaces have to be activated with the appropriate acessories, the choice depending on on the electrical conductivity of the component to be treated. While the Module Standard is ideally suited for the surface treatment of non-conductive substrates such as plastics, ceramics or glasses, the Module Nearfield was designed for the treatment of electrically conductive materials such as metals, CFRP, indium tin oxide (ITO) or conductive plastics.
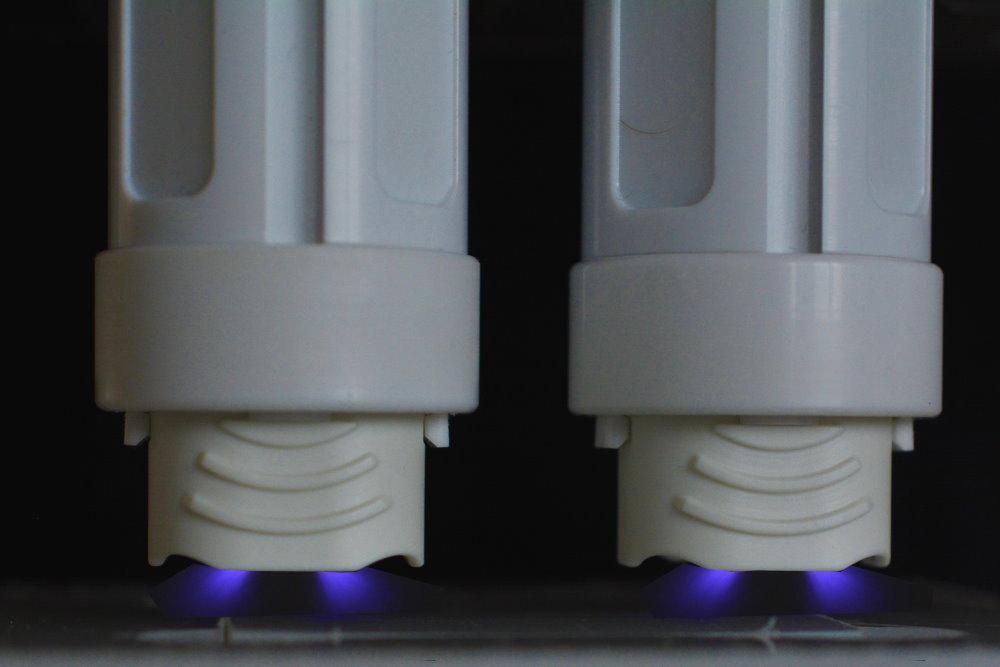
Modular design
With an average treatment width of 5 - 29 mm (CDA), the compact piezobrush® PZ3-i is very well suited for the pretreatment of adhesive grooves or for marking printing on low-energy materials. However, with other process gases such as nitrogen, treatment widths of up to 50 mm are possible. For many applications, even larger treatment widths are required. This is where the modular design of the piezobrush ® PZ3-i comes into play: It is very easy to string together the individual units at any time, so that larger treatment widths can be achieved. This enables flexible use of the device in a wide variety of industries and fields of application. Optimale adhesion results can be achieved with little effort.